By Mark Walker, director of business development with Kuert Concrete Inc.
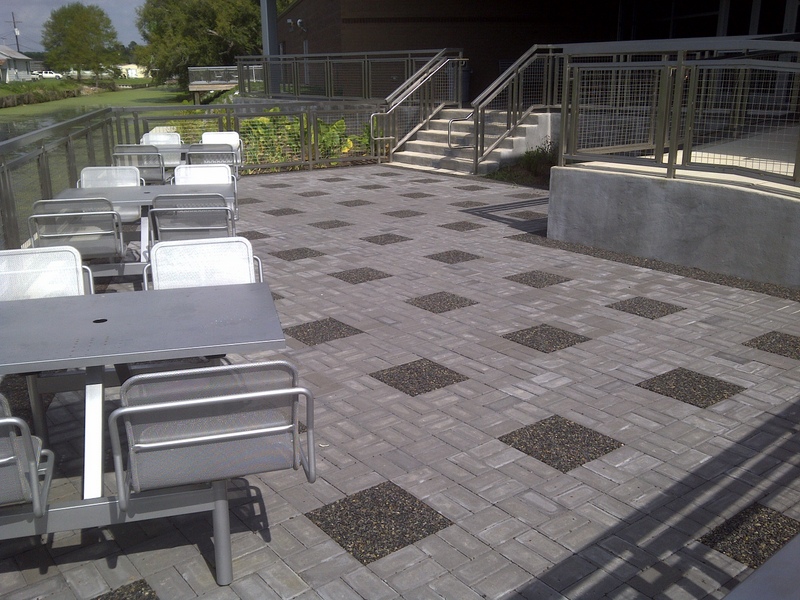
Xeripave, a pervious paver, used with permeable pavers. Photo courtesy of Xeripave Super Pervious Pavers.
Pervious, permeable, and porous pavers (the three P’s) often are used interchangeably by professionals without regard to their unique characteristics. They are, however, not the same.
There is an obvious and distinct difference between pervious, permeable, and porous pavers. Each possesses certain physical and aesthetic qualities that need to be considered prior to project design and installation. Careful consideration of site characteristics and project objectives will enable the owner to minimize stormwater runoff and maximize the water quality benefits that these products provide.
The goal in using these types of pavers for stormwater control is to limit runoff at the source, reduce downstream erosion, and improve water quality by filtering pollutants in the substrata layers. In the case of both pervious and porous pavers, this is partially achieved within the paver before water enters the layers below. With permeable pavers, water is circumvented around the paver, and the filtering process begins between the pavers in the void space filled with select aggregates. All three types require a similar compacted stone aggregate layering process beneath the surface to accept the stormwater and create a “reservoir” prior to the water percolating into the sub-grade or being piped away. This stormwater conveyance process is referenced by some paver manufacturers as the “paver system.”
While most rainfall events deliver less than 25 mm (1 in.), rainfall intensity always must be considered. Less than 25 mm over 15 minutes could cause more issues than 76 mm (3 in.) over 8 hours. Therefore, variances for stormwater runoff management primarily are for high-frequency, low-occurrence events. During a large storm event, the water table below any of these pavers can rise, preventing precipitation from absorbing into the ground. Paver system modifications generally are considered when determining the infiltration capacity of the sub-grade native soil and the depth of base rock for stormwater storage. Bioswales, rain gardens, and underdrain systems also are often considered during the design stages.
Permeable Pavers
Permeable pavers are composed of a layer of concrete or fired clay brick. The pavers are separated by joints filled with crushed aggregate. Permeable pavers are different from pervious and porous pavers in that rainwater passes around the paver opposed to through it. Permeable is a term used to describe paving methods for roads, parking lots, and walkways. This type of system allows the movement of water and air around the paving material. Water enters the joints between the solid impervious pavers and flows through the paver system. The aggregate in the joints provides infiltration as long as it is not plugged.
A periodic maintenance program is necessary for all three P’s to guarantee lasting stormwater conveyance past the paver layer. Per square meter, permeable pavers offer less stormwater infiltration than porous and pervious pavers, so to achieve the same results, a project would require additional pavers. Permeable pavers have an architectural appearance, and can bear both light and heavy traffic, particularly interlocking concrete pavers, excepting high-volume or high-speed roads.
Porous Pavers
Porous pavers are manufactured in a variety of designs and materials. Concrete turfblock for grass paving began in the mid-1940s, and plastic versions were invented in the late 1970s and early 1980s. Porous pavers generally are a cellular grid system filled with dirt, sand, or gravel. This system provides grass reinforcement, ground stabilization and gravel retention.
The grid structure reinforces infill and transfers vertical loads from the surface, distributing them over a wider area. Selection of the type of cellular grid depends on the surface material, traffic, and loads. The surface layer may be a compacted gravel or topsoil seeded with grass and fertilizer. In addition to load support, the cellular grid reduces compaction of the soil to maintain permeability, while the roots improve water infiltration due to their channels. Porous pavers, such as the reinforcement grids, also have been utilized in agriculture.
Pervious Pavers
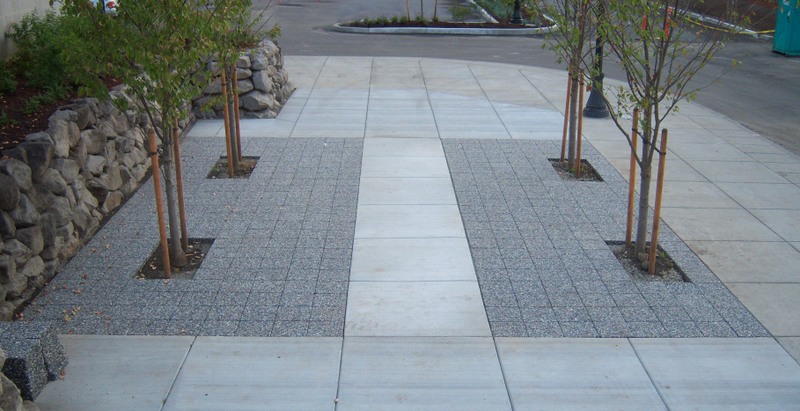
This example of pervious pavement surrounding several urban trees at an Amtrak station was provided by Xeripave Super Pervious Pavers.
Pervious pavers allow stormwater to percolate through the surface rather than running off into surrounding areas or storm drains. As water runs through, the pavers filter urban pollutants. Like grass, pervious pavers let the ground below breathe. These pavers also allow tree roots and their supporting microbes to interact.
Pervious pavers are not to be confused with homogenous binders mixed with backyard gravel or rubber compositions in a portable concrete mixer. These pavers are manufactured from natural stone and bonded together within a controlled factory environment using the latest innovations in chemical non-volatile organic compound polymers with ultraviolet inhibitors. Based on permeability assessed by the falling head test, pervious pavers feature the highest water infiltration rate — 10 times greater than pervious concrete and more than 90 times greater than permeable pavers. According to Low Impact Development 2010: Redefining Water in the City, published by the American Society of Civil Engineers, only 12% to 18% of a project’s total surface area in pervious pavers is typically required for optimal project drainage and stormwater management, greatly reducing the maintenance area
This space savings applies to the stormwater conveyance system beneath the pavers as well. When impervious surfaces, like standard concrete or asphalt, cover most of a project area, stormwater can be directed from the impervious surfaces to the pervious pavers to provide a cost-effective solution. Pervious pavers currently are code enforced within a number of municipalities in the western U.S., such as Reno, Nev. These pavers are used as a storm drainage filtration system that improves the quality of stormwater by capturing sediment, debris, and urban clutter. In addition to working as a filtration device, pervious pavers aid in vector control, helping to prevent viruses such as West Nile. Installed in stormwater catch basins, these pavers can reduce the number of mosquitoes by eliminating access to standing, stagnant water normally stored beneath the road surface.
Mark Walker is the director of business development for Kuert Concrete, the oldest central-batch mix operation in Indiana established in 1927. In addition to this position, Mark serves as a consultant with a number of Great Lakes professional organizations, such as individual state chapters of the American Institute of Architects, the American Society of Landscape Architects, as well as floodplain and stormwater management associations. As an educator in handling certain stormwater, erosion control, sustainability, and urban infrastructure issues, Mark also leads Kuert Supply Centers’ hardscape division.
Interesting article, not sure reference to infiltration rates is accurate(perhaps author can cite ASTM test method used?). Not sure Xeripave’s bonded aggregate has any long-term performance experience as a permeable pavement subject to wheel loading (certainly not comparable to concrete, brick, or asphalt). Little is known about the degradation of the “polymer” over time and its impact on water quality. Furthermore, unlike porous concrete or permeable concrete pavers, there is no recognized industry standard or ASTM method for the manufacturing or installation of polymer-bonded aggregate.
I have a field test of permeable clay pavers (ASTM C1701) calculating an infiltration rate of 720 inches per hour. I can’t imagaine needing anything higher than that.
Nice article and I agree that education about these systems are lacking and needed in the design community; however, it would have been nice to read more specifics about maintenance of the 3 systems, particularly methods and effectiveness of cleaning and how they impact infiltration rates during the life of the pavements. Long term durability is also a major factor that pavement designers need to consider and it would have been nice to see data comparing the 3 systems as well.
All good comments / questions, sorry for taking this long to return.
ASTM specification for the manufacture of super pervious pavers using a polymer binder would be a long time coming. Since the process is proprietary, why would the manufacturer want to divulge that info.
Also, ASTM specification on the mechanical property of the pavers could be a long time coming because of selecting the right testing method, that could be an evolving process. Case in point, although pervious concrete has been in use for several years, there is no ASTM test for measuring the compressive strength of pervious concrete. Compressive strength might not be so critical as thickness of the concrete slab that is poured.
As for the infiltration test, the testing was done using a dropping head test that, and performed on different pavers using different sized aggregate. The crux of the matter is that with a void capacity of up to 40%, it can be expected to have a high infiltration rate and can be used in application where a grate might be the only viable alternative. Additionally, third-party engineering tests have recently released runoff co-efficient testing….to be “0”.
In regards to the comparison to concrete, asphalt, concrete or clay paver surfaces, one must first consider that a 33%+ void capacity must be taken into consideration when choosing the thickness of the Xeripave pervious pavers product to be used in a specific application. A lot of issue is put into whether a fire truck can drive on it, which is not a problem, but more of a marketing issue. The problem really resides in not the ground pressure of the fire truck, but the ground pressure exerted by an outrigger from the truck. The outrigger supported on a pad (which one would assume would be a normal procedure) exerts about 175 psi. Compressive strength of Xeripave is around 2000 psi which is more than adequate. The real issue is whether the rock foundation supporting the paver is adequate to support the outrigger.
Thank you.
I am interested in creating garden paths for wheelchairs. Paved walkways on a hill. Can be expensive and the 12:1 slope requirement makes for long runs that direct erosive runoff. I thought porous pavers were the most cost effective solution. Unfortunately the market seems to be moving away from this in Michigan. What do you suggest?
ADA dictates 1:12, which is a 5% grade Hugh. Please advise what part of Michigan you’re from and I might be able to suggest a couple of local project sites where “pervious” pavers have been used. If not, then please feel free to contact me directly and I’ll assist you. (574) 232-9911
Any chance pervious pavers can be used in AP taxiways? Perhaps the 18% can distributed in such a way as not become a load bearing issue with heavy aircraft.
I never argue with experts so consider this a request for instruction: a 1:12 grade is 5%? I would have guessed naively that 5% would be a 1:20 (5:100). How is the equivalence calculated?
When designing HC access, we use a rise of 1:12 that would be calculated to percentage as rise of 1 divided by run of 12 obtaining 0.08333333 or 8.333%. (A 5% grade being less, would clearly meet ADA and be even easier to negotiate).
Thank you Scott. Outside of my in-haste trivial oversight, it has come to my attention that there is now a new pervious kid on the block…Percoa. This is a 2.0 version of the earlier innovative paver noted above. Showing promising results after a 5-year battery of field tests conducted by MNDOT. More to come.
Superb article! I am very thankful to you for sharing this relevant topic. its well describes permeable paving how much this beneficial for the earth.
I thought it might great to define a section that was already different from the rest of the room. Well, that and sympathy. I think the herringbone pattern took way more time and effort than my tile guy anticipated, so when he asked if I wanted the sunken area to be straight or herringbone I told him straight.
Emma
https://www.eaglerockexcavating.com/